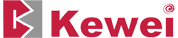
1 Product application and introduction
Molybdenum has good mechanical properties and resistance to glass solution corrosion at high temperatures (1100-1650°C), and is widely used in point light sources, electronic devices, heating elements, and glass fiber processing industries. However, molybdenum products begin to be oxidized at a temperature of about 400°C, and the oxidation rate gradually accelerates as the temperature increases. Therefore, traditional molybdenum and molybdenum alloy products often need to be used in a vacuum environment or an inert gas protective environment. , to solve the oxidation problem of molybdenum and molybdenum alloy products at high temperatures, and limits the use of molybdenum and molybdenum alloy products in high temperature environments and aerobic environments. The coated molybdenum products and coated alloy products produced by Luoyang Kewei Tungsten and Molybdenum Co., Ltd. can form an effective protective layer to isolate oxygen penetration at high temperatures, thereby effectively solving the problem of molybdenum and molybdenum alloy products being exposed to high temperatures and atmospheric conditions. Oxidation problems in the environment, Kewei coated molybdenum and molybdenum alloy products are shown in Figure 1
Figure 1 Schematic diagram of Kewei coated molybdenum and molybdenum alloy products
When the coating is at 700°C, an oxide film forms on part of the surface, but it is neither dense nor continuous. At this time, there will be a slight loss of molybdenum and its alloy matrix. This is mainly due to the fact that no continuous oxide film is formed on the surface of the coating. When the temperature is greater than 1000°C, a continuous dense oxide film will form on the surface, thus forming good protection for molybdenum and its alloy matrix.
Figure 2 Dimensional schematic diagram of coated electrodes
4 Coating properties
4.1 Coating characteristics
4.2 Analysis of coating test results
Kewei coated electrodes are used in glass melting furnaces in Taiwan. The space temperature is 1450-1500°C. The use time is 192 hours. After use, there is no defect or damage to the coated electrode structure. After use, the appearance of the electrode is See Figure 3. It can be seen from the figure that the coated electrode has a complete structure at this temperature, and there is no phenomenon of coating peeling or damage. Figure 4 shows the microscopic morphology of the coating. It can be seen from the figure that the coating and the substrate are closely connected, without pores and cracks, and there is a transition layer between the coating and the substrate. That is, the connection method between the coating and the substrate is metallurgical. Connection, the connection method is firm and tight, not easy to fall off and damage
Figure 3 Schematic diagram of coated electrode after use
Figure 4 Microscopic morphology of the coating
5 storage and transportation instructionsFigure 5 Schematic diagram of smoke-free box for packaging
2. Figure 5 Schematic diagram of fumigation-free box for packaging5.2 5.2 transportation
Considering that molybdenum-coated electrodes are relatively hard and brittle, please handle them with care during transportation and storage to avoid collisions, and do not press them heavily. Take measures to prevent moisture and rain to avoid oxidation and deterioration of the uncoated parts of the coated electrodes.
5.3 storage
1. Coated electrodes that are not installed in time after unpacking and inspection must be repackaged according to the original packaging method, and must be handled with care, and bumps and impacts are strictly prohibited.
2. Make sure that the coated electrode is stored in a dry environment with an ambient humidity of less than 50% and a temperature of less than 25°C (optimal temperature 15°C-25°C) to avoid oxidation of the uncoated areas of the coated electrode.
3. If stored in a humid and high-temperature environment for a long time, oxidation, corrosion, and mildew will occur in the uncoated areas of the coated electrode.