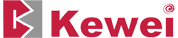
Zirconia ceramic particle reinforced molybdenum electrode
1 Preface
Zirconia molybdenum electrode is a metal oxide solid solution material. This material is a metal-based ceramic dispersion-reinforced composite material formed of zirconia ceramics and molybdenum metal. The ultra-fine zirconia ceramic powder is evenly dispersed among the molybdenum metal grains. , which limits the growth of metal grains at high temperatures, thereby increasing the recrystallization temperature of molybdenum metal. It has high strength and low creep rate at high temperatures, and is called an ODS material. Although this type of molybdenum electrode has been used for many years History, but it was only really used in the glass manufacturing industry. For glass production processes involving highly corrosive glass melts, molybdenum is added with small amounts of zirconium oxide (ZrO2) to enhance the properties of the pure material. MoZrO2 has extremely strong anti-corrosion properties for the glass melt, and is also more resistant to creep than pure molybdenum. The main application areas of MoZrO2 include glass production for the solar industry and the container glass industry. The solar glass production process utilizes corrosive refining agents such as antimony oxide. It destroys the particulate structure of pure molybdenum, causing rapid electrode wear and breakage. MoZrO2 is able to withstand this corrosive environment. MoZrO2 significantly reduces electrode corrosion even in brown and green container glasses。
2 experiment method
The test raw materials are molybdenum powder and zirconia powder with purity >99.95% (in compliance with relevant standards). The morphology pictures are shown in Figure 1 (a) and (b). The mixing ratio is 99.5~95% molybdenum powder and 0.5~5% zirconia powder (mass percentage). The test process flow is shown in Figure 1. Two powders of different proportions are mechanically mixed (including the addition of molding agents, etc.), and then pressed and molded under the same cold isostatic pressure, and then sintered. The density of the sample after sintering is about 95%, and the chemical composition is as shown in the table 1; After the sample is tested, press it to obtain an excellent microstructure and higher density. The pressure processing method used in this experiment is free forging. The samples were tested for metallography and density before and after forging, and the mechanical properties of the samples after forging were tested. The density test used Archimedes' principle and an electronic balance without an Archimedes device; the metallographic test used MA- 100 type Nikon optical microscope (the preparation of metallographic samples is: sampling-mechanical grinding-polishing-erosion, etc.); the mechanical properties test uses the WDW100 microcomputer-controlled universal testing machine。
表1氧化锆钼电极化学成分(质量分数,%)
Al | Ca |
Cu |
Fe |
Cr |
Ni |
Mg |
Si |
C |
N |
<0.0005 |
<0.0010 |
<0.0005 |
<0.0020 |
<0.0005 |
<0.0020 |
<0.0005 |
<0.0010 |
<0.0020 |
<0.0010 |
Figure 1 Zirconia molybdenum electrode process flow
Figure 2 Molybdenum powder and zirconia powder SEM
3.1 Microstructure after sintering
The raw materials used in this test are all high-purity (purity greater than 99.95%) powder materials, so the purity of the material after sintering must be above 99.95%, because the material has been sintered at high temperature, and high-temperature sintering is not only a way to increase the strength and density of the material. The process is also a material purification process (low melting point impurities volatilize in a high temperature environment). This article only shows a relatively good set of relevant data for adding proportions of zirconia. Figure 3 is a set of microstructure pictures of zirconia molybdenum electrode after sintering. Figure 3 (a) and (b) are pictures of the microstructure of zirconia molybdenum electrode after sintering at 200 times and 1000 times respectively. As can be seen from Figure 3(a), the microstructure of the zirconia molybdenum electrode after sintering is fine and uniform, with an average grain diameter of 15 μm, and the zirconia particles are evenly distributed on the grain boundaries; Figure 3(b) clearly shows that the zirconia particles are smaller than 5μm spherical morphology is evenly distributed on the molybdenum grain boundaries。
Figure 3 Microstructure picture of zirconia molybdenum electrode after sintering
3.2 Microstructure pictures after forging
Figure 4 Microstructure picture of zirconia molybdenum electrode after forging
3.3 Mechanical propertiesTable 2 Mechanical properties of pure molybdenum electrodes and zirconia molybdenum electrodes of the same specifications
|
tensile strength /MPa |
Yield Strength /MPa |
Elongation after break /% |
Zirconia molybdenum electrode |
584 |
517 |
35.7 |
Pure molybdenum electrode |
536 |
459 |
29.1 |
American Standard |
515 |
450 |
10 |